Transparent Production
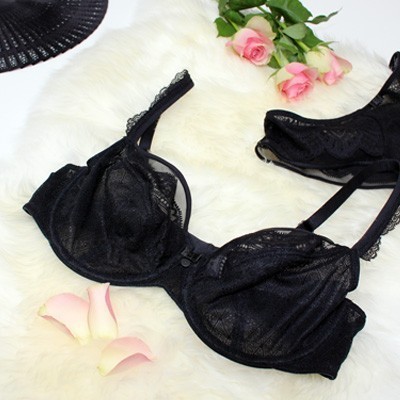
Dear customers,
Every day around the world hundreds of employees in our own manufacturing facilities sew Anita and ROSA FAIA products with the very best fit, excellent comfort and unrivalled quality. It is a demanding, but also worthwhile job!
That is why we owe it to the people who work for us to actively take responsibility for their workplaces and working conditions – wherever they are. And specifically in locations like Thailand and Myanmar.
Yours, Georg Weber-Unger
4th Generation Company Owner
Manufacture
The process starts with an idea – and ends in a finished product!
Everything at ANITA – with very few exceptions – from the initial sketch to the finished product comes from a single location. Despite the fact that we have become a global and also quite large company, many things are still done like in a small workshop, i.e. a true artisan's workplace!
Producing an Anita bra or swimsuit is very time and labour-intensive. Dozens of individual work steps and tasks are needed to make a perfectly fitting and comfortable Anita garment.
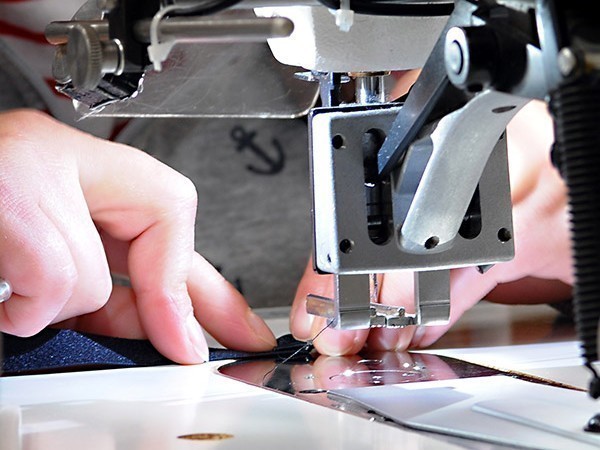
Cutting & Sewing Rooms
Once the item has been successfully and thoroughly tested, it will then go into production. The first step here is the creation of a cutting pattern. Next, the fabrics are placed on a giant worktable in four layers and the various garment components are cut out: the cup, the back, the bridge, the straps, etc.
Then our seamstresses in the many facilities around the world bring the various components of the bra ‘to life’. Their expert finesse and years of experience ensure that the bra gets its hook & eye fastener, that the underwire is threaded into the channel or that the armholes are edged. That is how a finished bra or swimsuit gets constructed piece by piece.
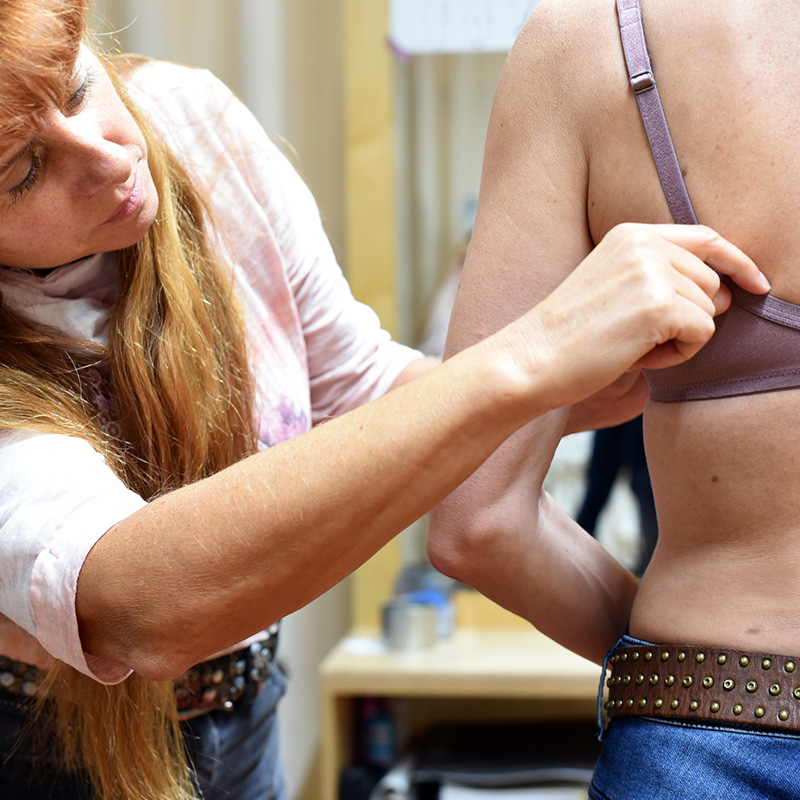
Cuts & Samples
Once all the items and series have their final approval, a matching cutis created for each size and each cup. Depending on the article, that can mean up to 50 individual cuts. Other companies take a much easier route by simply 'upgrading'. That means they create a base cut in e.g. size 75 C, and then just add a set amount of millimetres per cut for any size above. That may be a much simpler solution, but it often results in an inferior fit. We really pick up each individual cup and size combination and make sure we develop the very best. Our cutters work on the PC and on real women, until absolutely everything fits perfectly!
All Anita products are tested over and over again on various product testers and models and are thoroughly tested in everyday life. It’s not easy: as you can imagine – just like any woman, all our product testers and models are different. They might even move a size up or down after holidays! That is why we take measurements and make corrections on an ongoing basis – but that's just what you have to do if you want to create an unrivalled fit.
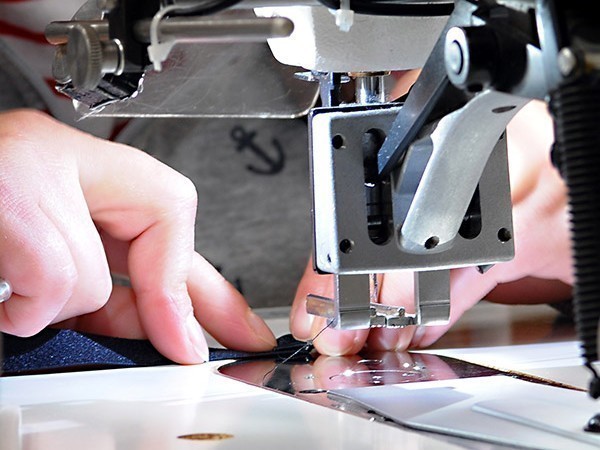
Cutting & Sewing Rooms
Once the item has been successfully and thoroughly tested, it will then go into production. The first step here is the creation of a cutting pattern. Next, the fabrics are placed on a giant worktable in four layers and the various garment components are cut out: the cup, the back, the bridge, the straps, etc.
Then our seamstresses in the many facilities around the world bring the various components of the bra ‘to life’. Their expert finesse and years of experience ensure that the bra gets its hook & eye fastener, that the underwire is threaded into the channel or that the armholes are edged. That is how a finished bra or swimsuit gets constructed piece by piece.
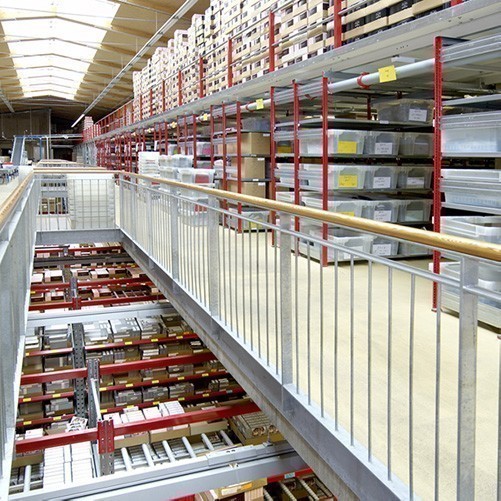
Final Quality Control, Storage & Shipping
Every finished Anita or ROSA FAIA product undergoes a 100% final quality check before it leaves our premises. The material, seams and the exact measurements of each item are visually checked by experienced employees. That is how we can guarantee absolutely reliable and excellent products that you will be able to enjoy for a long time.
Products manufactured around the world make their way back to our logistics centre in Kufstein, Austria. There we store around 1.2 million shapewear and swimwear articles in countless cup and size combinations, ready to ship to our many trading partners around the globe. The desired article generally reaches the retailer, and therefore you, within two days!
Production in our own facilities
As a 100% family-run business, ANITA operates all production companies in compliance with European standards, with its own management personnel.
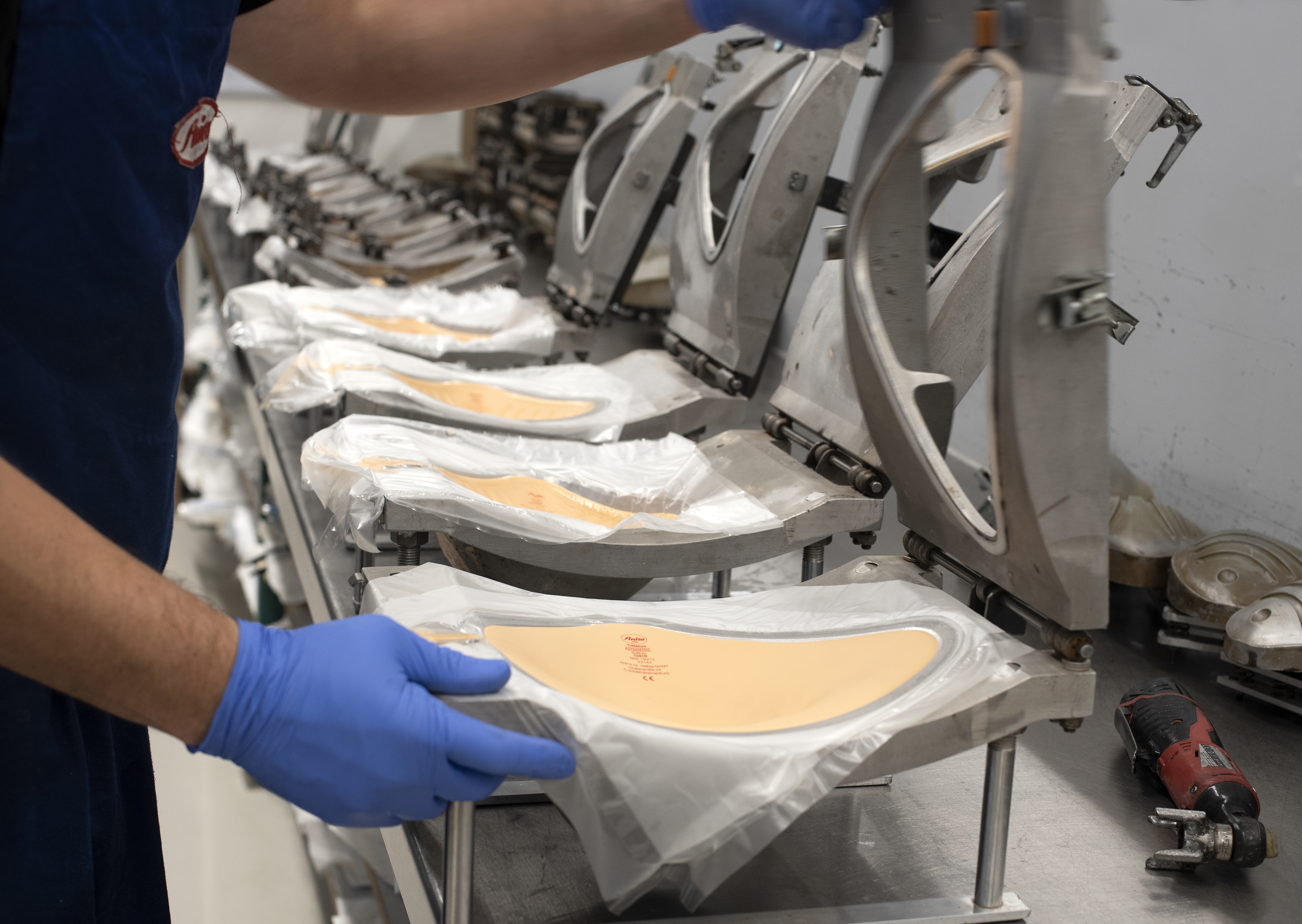
We ensure optimal working conditions for everyone working in our facilities – be it in Germany, Portugal, Austria, Czech Republic, Thailand or Myanmar.
In developing countries like Thailand or Myanmar, our quality requirements for work places are particularly high.
That is just one reason why our products are always premium quality – the other is that we buy our raw materials from specialist manufacturers in Europe only.
We are rewarded with happy employees and unsurpassed product quality.
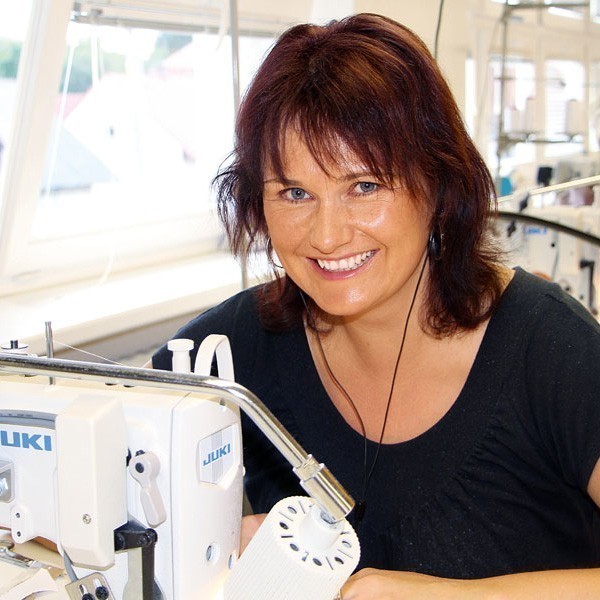
Local work conditions
Respect for workers is part of the general attitude and business philosophy of ANITA owner Georg Weber-Unger.
At our manufacturing facilities in Portugal and the Czech Republic, and specifically in our Thai and Burmese locations, these are a top priority. Clean, bright and hygienic work places with state-of-the-art equipment and optimal climate control are a matter of course. Just like medical attention and financial support in case of illness.
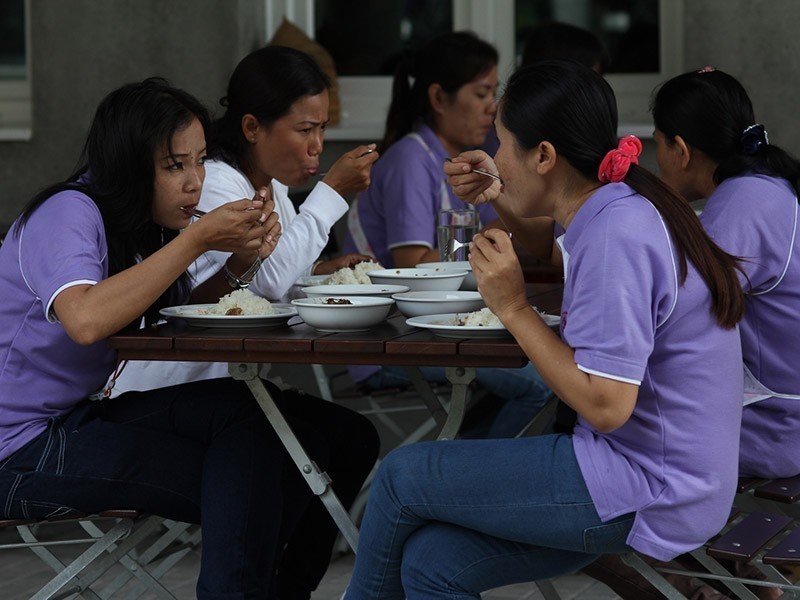
Owner Georg Weber-Unger personally ensures that our workers receive meals. The quality and nutritional value of the meals served is very important to him.
All our facilities have regular working hours. There are guaranteed break times and fair holiday models, and we don't work on weekends and public holidays – a rare bonus for workers in Asia.
We also offer our employees regular and easy transport options to and from work:
All our facilities are located in beautiful surroundings and natural environments, away from typical industrial areas.
Here you can see the working conditions at our facilities in Thailand and Myanmar for yourself, and get a chance to look behind the scenes of our Asian manufacturing locations!